Is polycarbonate or polyester better for your application?
A graphic overlay is the visual interpretation of a membrane switch that is exposed to the external environment – the part that is seen, touched, and cleaned. It is typically printed on the back side (second surface) of a transparent or semi-transparent material, and may include embossed buttons for functionality. Polyester (PET) and polycarbonate (polycarb, PC) are the most commonly used films in graphic overlay construction. These products possess properties such as durability and processability, along with aesthetics, which are all required for its application.
Your graphic overlay material choice depends on multiple factors such as:
- interface requirements
- environment
- durability
- expected performance in the final application
Flex Life, Actuation Life and Switch Life
These terms are used to describe how many times a switch button can be flexed before an overlay fails. When a failure occurs, the overlay will be deformed with a loss of functionality. Flex life can be influenced by many factors, but in almost all cases PET will last longer than PC. Most overlays are between 5–15 mils thick. Any higher in thickness, durability becomes more important than tactile feel.
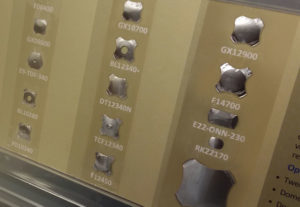
Embossing the overlay will reduce the actuation life of both films, with the severity depending on the emboss style and the distance the material must flex to activate the switch. Metal domes (see photo) can be added to embossed keys for added durability.
Abrasion Resistance
The availability of PC in a variety of textures give the film built-in resistance to abrasion without the assistance of a hard coat, although there are hard-coated PC options available for additional durability. PET, on the other hand, must be hard-coated to endure normal use and is available in several textures. Polyester also offers a more consistent gloss and textured surface. Once it has the coating, however, it is much harder to scratch than regular PC.
Chemical Resistance
The efficacy of PET to resist chemical abrasion largely surpasses that of PC. PET is chemical resistant to household cleaners, graffiti-resistant, resistant to alcohol and acid, and overall has a greater resistance to a broader range of chemicals than polycarbonate. PC does have chemical resistance but it is limited, and overall is less desirable for harsh environment use. Hard-coated PC, however, will resist periodic first surface exposures, but this will only slow down the effects of long-term exposure that will attack uncoated edges and penetrate the hard-coating.
Flammability
While most PET films do not present a significant flammability hazards, most will burn when placed under suitable conditions. PC is generally regarded as “flame-resistant”, and there are even flame-retardant films that have been designed specifically with excellent flame-resistant thermal, electrical insulation, and mechanical properties.
Appearance
Visual appearance is where PC vastly overshadows PET. PC is available in a much a wider range of thicknesses and textures and finishes, such as gloss and matte versions of fine, suede, and velvet surface textures. It is also more clear than PET in higher thicknesses, allowing more vibrant colors and closer PMS color matches. While both have the same gloss level selections of 100, 90, 75, 66, 40, 35, and 20%, PC has the edge cosmetically. A variety of options can be hard for designers and marketing teams to resist.
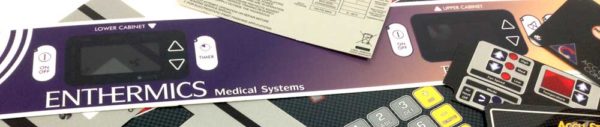
Ease of Production
PET is harder than PC to process. It needs stabilized to resist shrinking during low temp ink curing conditions, and is more prone to splitting at the edge than PC. PET also has a higher material memory, meaning that its elastic properties want to go back to its original shape after being embossed. To emboss PET correctly high temperatures and dwell times are necessary to force it to keep its shape. While you will not see the effects of processing directly in your finished part, it will affect the lead time from your supplier, as PET parts will often take longer to make, and because PC is so much easier to work with, it often equates to lower costs.
PET material is the most commonly used base material for graphic overlays. It cannot be torn and all membrane circuitry must be done with polyester, and withstand higher temperature but is flammable. PC is flame retardant, meets the vertical burn test requirements, and is more moldable. Both materials have their own advantages and are the two best materials available on the market. When considering which material is right, weighing these advantages is important.
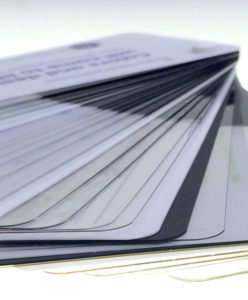
Polyester (PET) vs Polycarbonate (PC) Film Comparison For Graphic Overlays | ||
PET | PC | |
Flex Life/Overall Durability | X | |
Tear Resistance | X | |
Chemical Resistance | X | |
Allows for Membrane Circuitry | X | |
Abrasion Resistance *Standard Material | X | |
Abrasion Resistance *Hard-coated Material | X | |
Flame Retardant | X | |
Variety of Finishes & Textures | X | |
Clarity in Higher Thicknesses | X | |
Ease of Processing | X | |
Cost | X |
As you can see, choosing between Polyester (PET) and Polycarbonate (PC) films for a graphic overlay can be somewhat complicated. Overall, polyester is suited for long-term use with high reliability, while polycarbonate is best when appearance or cost is most important, or usage is considerably low. Of course, there will always be exceptions to the rule, and all aspects of each material should be considered carefully before making a final decision for your application. If you have any questions concerning which material is best for you, please reach out by phone at 260-748-0577 or email sales@gographicsoutput.com. Graphics Output is always willing to help!